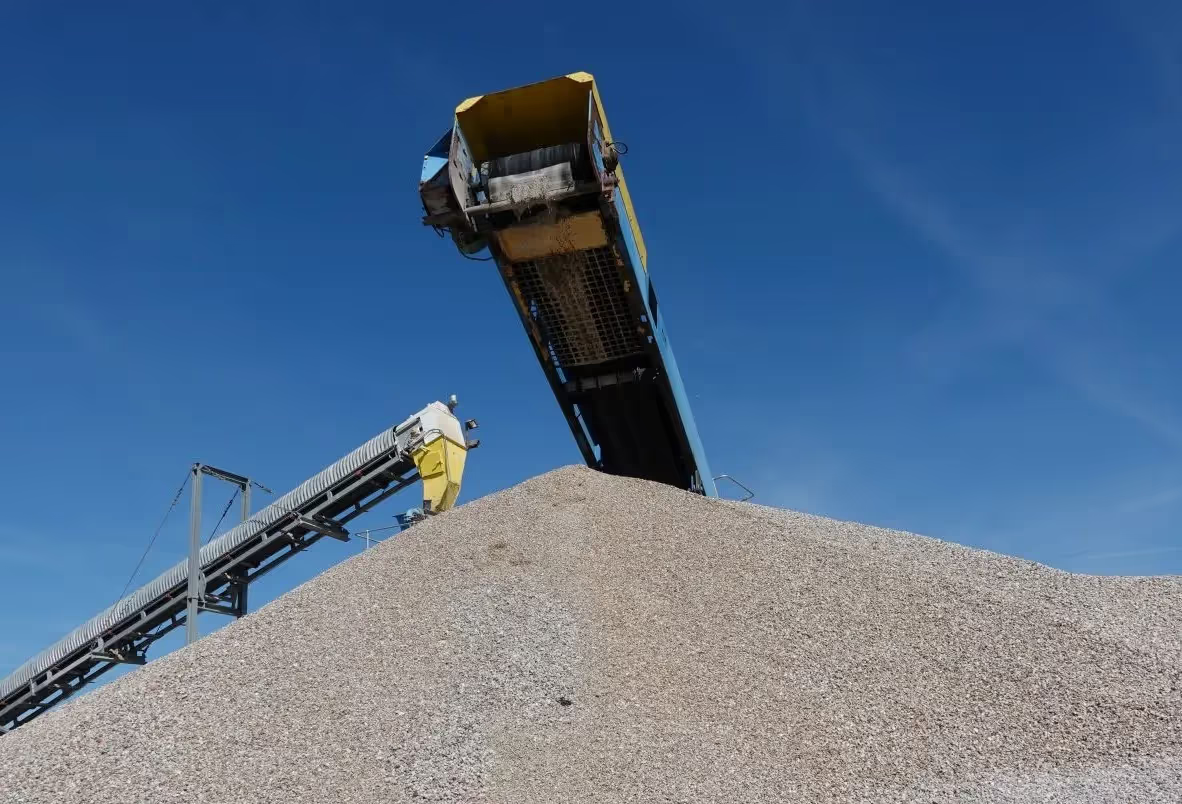
Construction is one of the largest and most consuming industries of natural resources in the world. One of these resources, concrete, is the most used building material in the world, but its production and disposal have a significant environmental impact.
The building sector generates around 46 million tons of waste per year, of which more than 85% comes from deconstruction and rehabilitation works. The material recovery rate is 67%, all waste combined, with a strong increase expected with the implementation of the REP Building in 2023. (Source: FFB)
In addition, the new Environmental regulations known as RE 2020, which came into force last January, has imposed major changes for building manufacturers - especially in terms of recycling (and not only concrete).
So how can we make the concrete industry more sustainable? The answer can be found in the concrete recycling.
What is concrete recycling?
Concrete recycling involves the collection of concrete debris from demolition sites that is then crushed and reused as aggregate in the manufacture of new concrete or for other construction applications. This practice is increasingly being adopted around the world due to its numerous environmental and economic benefits.
Why recycle concrete?
Concrete recycling offers numerous advantages. From an environmental point of view, it makes it possible to reduce the exploitation of new natural resources, thus reducing the carbon footprint of the construction sector. In addition, it avoids the landfilling of concrete waste, thus reducing the impact on landfills and groundwater pollution.
From an economic point of view, the recycling of concrete saves on the costs of transporting and discharging waste, as well as on the purchase of virgin materials. In addition, the use of recycled concrete can also offer advantages in terms of the performance of the finished product, such as better resistance to certain environmental conditions.
How is concrete recycled?
The concrete recycling process usually starts with the demolition of existing concrete. Then, the concrete debris is sorted to remove contaminants, such as steel and other building materials. The remaining concrete is then crushed into aggregates of various sizes, which can be used in the production of new concrete or for other construction applications, such as road backfilling or earthworks.
The challenges of recycling concrete
Despite its many benefits, concrete recycling is not without its challenges. The quality of recycled concrete can vary depending on the age and composition of the original concrete, which can affect the performance of the new concrete. In addition, the presence of contaminants can also affect the quality of recycled concrete.
However, with the development of more advanced sorting and crushing technologies, these problems can be overcome, making concrete recycling an increasingly viable and attractive option for the construction industry.
EPR: a significant impact on concrete recycling
La Extended Producer Responsibility (EPR) in the Concrete Construction Materials sector (PMCB) has a significant impact on concrete recycling. This initiative aims to encourage producers to design more sustainable products and to participate actively in their end of life, by encouraging them to reuse, recycle or recover the waste from their products.
With regard to concrete, the implementation of REP PMCB allows recycling rates to be gradually increased. Producers find themselves more motivated to develop more efficient methods of collecting and treating concrete waste, thereby reducing the environmental impact of concrete production. This initiative has also stimulated innovation in the creation of new recycled concrete products, contributing to the circular economy and reducing dependence on natural resources.
Herve de Maistre, the president of VALOBAT, did us the honor of evoking in an episode of our podcast the REP PMCB and the Agec law, but also the concept of the eco-organization and its detailed functioning: exemption, scale, redistribution principles... Everything is going well!
Good practices
Here are some best practices to follow for efficient and eco-responsible concrete recycling.
1. Preliminary triage
Sorting is a key step in the recycling process. It's about separating concrete from other construction and demolition waste. Careful sorting eliminates contaminants that could affect the quality of recycled concrete. Arnaud Rongier, co-founder of EndLess band (ex Big Bag 'n Go), tells us about his solution for collecting your construction waste and recovering it, in our podcast”The Builders”.
2. Ensure adequate particle size
It is important to control the particle size of recycled concrete. Adequate particle size can improve the quality of recycled concrete and make its use more flexible. Screening techniques can be used to obtain a uniform particle size.
3. Use of adapted crushing equipment
The quality of recycled concrete depends largely on the crushing technology used. The use of modern and efficient crushing equipment can improve the quality of recycled concrete, thus broadening its range of potential applications.
4. Respecting quality standards
The quality of recycled concrete must be monitored and maintained in accordance with industry standards. This requires regular testing to ensure that recycled concrete meets quality and performance standards.
5. Awareness and education
Promoting awareness and education about the benefits of concrete recycling is crucial to encouraging its adoption in the construction industry. Workshops, seminars, and trainings can help construction professionals understand the importance of concrete recycling and learn best practices.
Concrete recycling is a significant advance towards a more sustainable construction industry. With its numerous environmental and economic advantages, it offers a promising solution to the environmental impact of the construction industry. It is essential that industry players continue to invest in concrete recycling technologies and promote sustainable building practices to ensure a greener future for our planet.